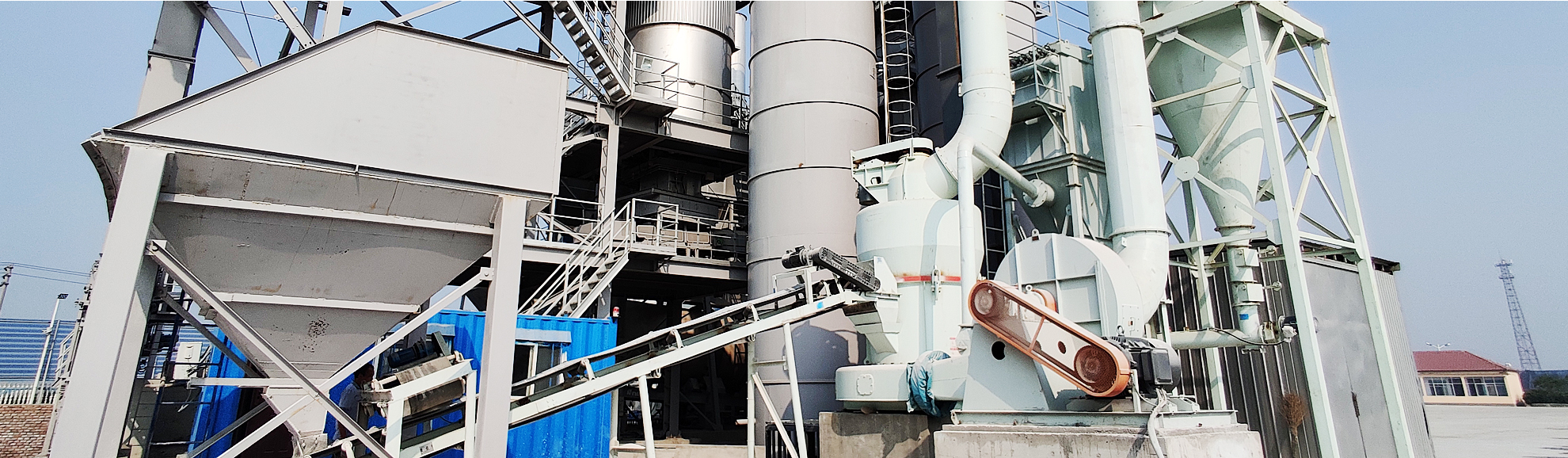
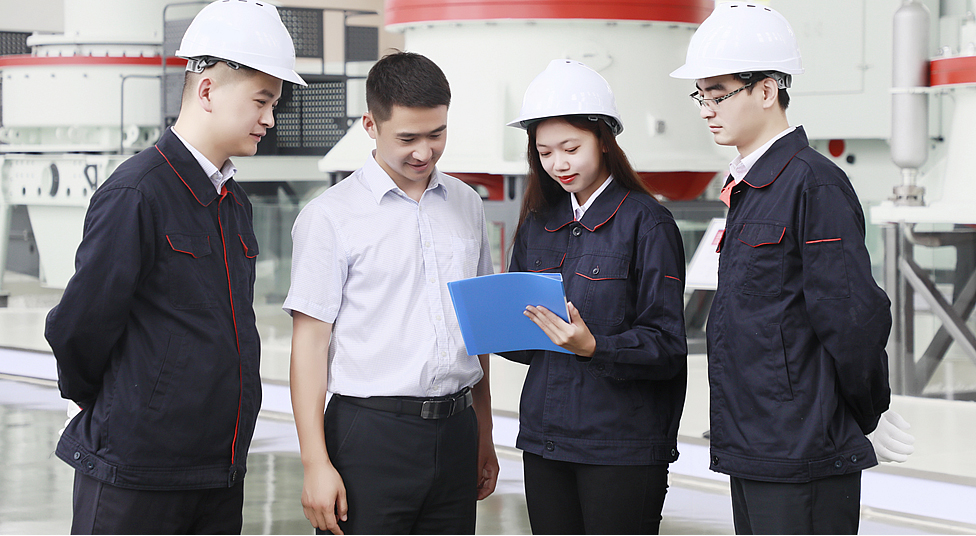
ball mill atomisation
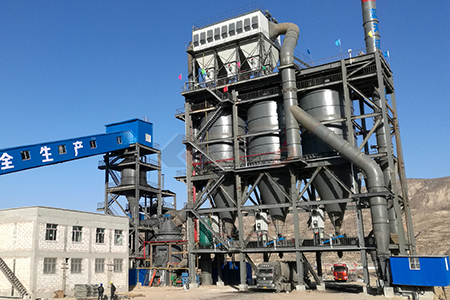
Producing Metal Powder from Machining Chips Using Ball
2023年6月27日 The optimum ball mill parameters to achieve a small particle size of 0.056 µm include a ball mill speed of 500 rpm, a milling time of 10 h, and a ball-to-powder ratio (BPR) of 10:1. These settings are sufficient for obtaining better results.
More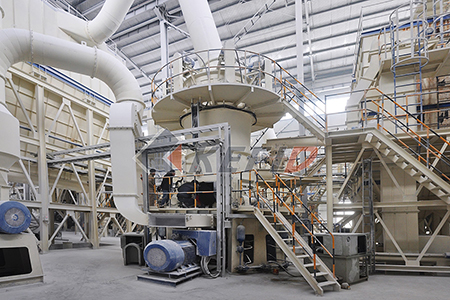
Mechanochemical preparation of single atom catalysts for
2023年3月1日 In this review, we systematically summarized the methodology and principle of ball milling strategy for the preparation of SACs for the first time, which include the solvent-assisted ball-milling strategy, solvent-free ball-milling strategy, and ball-milling abrasion-thermal atomization joint strategy.
More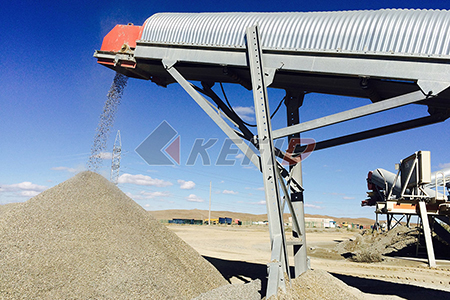
Materials Development Using High-Energy Ball Milling: A
2022年6月17日 High-energy ball milling (HEBM) of powders is a complex process involving mixing, morphology changes, generation and evolution of defects of the crystalline lattice, and formation of new phases.
More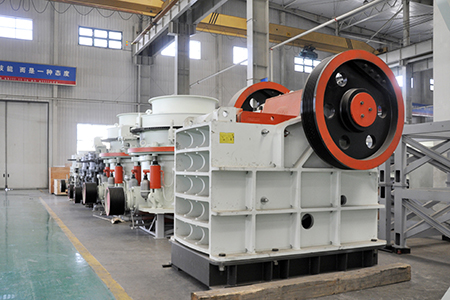
Ball milling process variables optimization for high-entropy
2023年9月1日 In this study, the influence of ball milling variables (PCA type, PCA amount, ball milling time, and ball milling speed) on the onset of solid-solution, grain size, and particle size of a model HEA (AlCoCrFe) is systematically evaluated.
More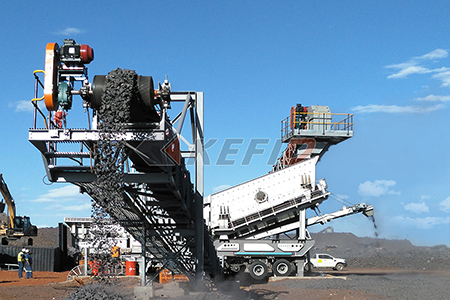
Control the Mechanochemical Energy of Ball Milling To
2023年10月3日 According to collision theory and the strength of materials, it was calculated that the glass would not be broken by ball milling at 146 r/min. Due to mechanochemistry reactions of organic pollutants on the surface, a large number of hydroxyl and ethylenic bond groups were decomposed, producing harmless organic gases, such as propane and ethyl ...
More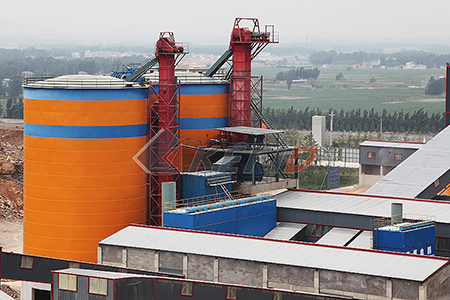
High-temperature ball milling: An efficient method to
2024年3月1日 This study proposed high-temperature ball milling (HTBM) to modify irregular titanium and its alloys powder for AM, such as hydrogenation-dehydrogenated titanium (HDH Ti), and the ball milling mechanism was revealed. The results showed the irregular HDH Ti powder gradually turning into nearly spherical and flake structures.
More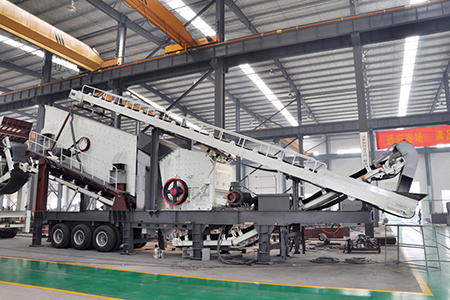
Effects of ball milling on powder particle boundaries and
The Cu-0.25 wt% Al powder was prepared by water atomization, followed by internal oxidation, diffusion, and reduction. Dispersion-strengthened copper powders with internal nano-Al 2 O 3 were obtained as starting materials. The initial powders were ground via a high-energy planetary ball mill with a ball-to-powder weight ratio of 3:1 for 1 h.
More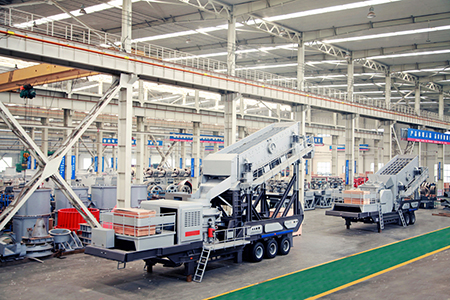
Direct Mechanocatalysis: Using Milling Balls as Catalysts
2020年4月21日 High-speed ball-milling: Direct mechanocatalysis is a new catalysis concept using high speed ball milling conditions. The surface of the milling balls is the catalytic active site, hence the recovery of the catalyst is convenient and efficient. Being a solid state technique, solvent related problems are omitted.
More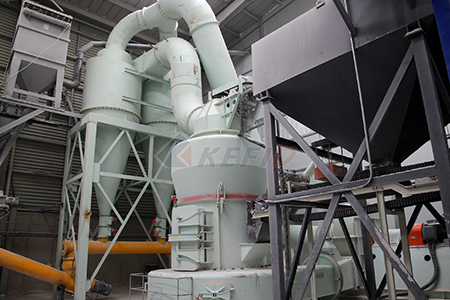
Aromatic substitution in ball mills: formation of aryl chlorides
Aryl chlorides and bromides are formed from arenes in a ball mill using KHSO5 and NaX (X = Cl, Br) as oxidant and halogen source, respectively. Investigation of the reaction parameters identified operating frequency, milling time, and the number of milling balls as the main influencing variables, as these de.
More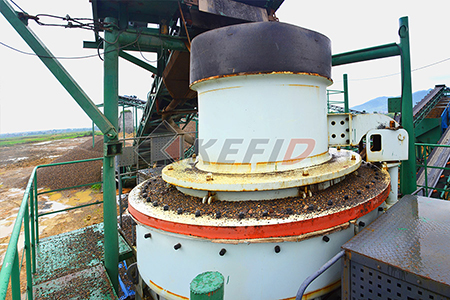
(PDF) Producing Metal Powder from Machining Chips Using Ball
2023年6月27日 Nevertheless, parameter factors, such as the type of ball milling, ball-to-powder ratio (BPR), rotation speed, grinding period, size and shape of the milling media, and process control agent...
More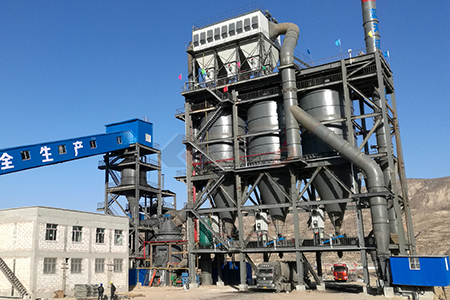
Producing Metal Powder from Machining Chips Using Ball
2023年6月27日 The optimum ball mill parameters to achieve a small particle size of 0.056 µm include a ball mill speed of 500 rpm, a milling time of 10 h, and a ball-to-powder ratio (BPR) of 10:1. These settings are sufficient for obtaining better results.
More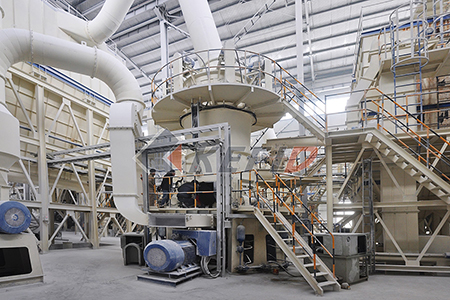
Mechanochemical preparation of single atom catalysts for
2023年3月1日 In this review, we systematically summarized the methodology and principle of ball milling strategy for the preparation of SACs for the first time, which include the solvent-assisted ball-milling strategy, solvent-free ball-milling strategy, and ball-milling abrasion-thermal atomization joint strategy.
More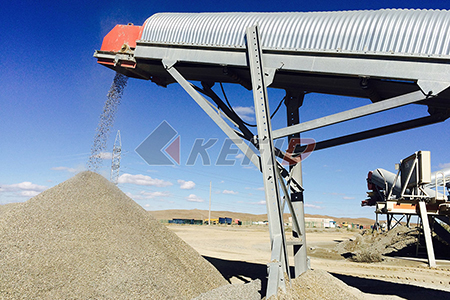
Materials Development Using High-Energy Ball Milling: A
2022年6月17日 High-energy ball milling (HEBM) of powders is a complex process involving mixing, morphology changes, generation and evolution of defects of the crystalline lattice, and formation of new phases.
More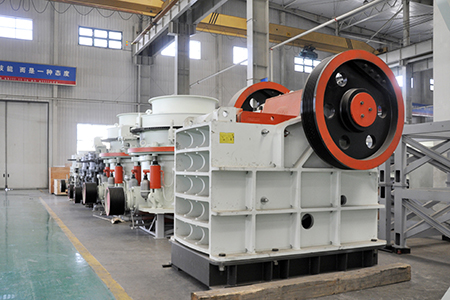
Ball milling process variables optimization for high-entropy
2023年9月1日 In this study, the influence of ball milling variables (PCA type, PCA amount, ball milling time, and ball milling speed) on the onset of solid-solution, grain size, and particle size of a model HEA (AlCoCrFe) is systematically evaluated.
More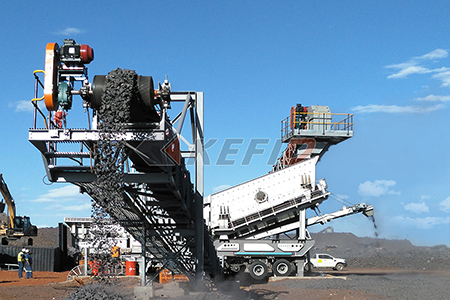
Control the Mechanochemical Energy of Ball Milling To
2023年10月3日 According to collision theory and the strength of materials, it was calculated that the glass would not be broken by ball milling at 146 r/min. Due to mechanochemistry reactions of organic pollutants on the surface, a large number of hydroxyl and ethylenic bond groups were decomposed, producing harmless organic gases, such as propane and ethyl ...
More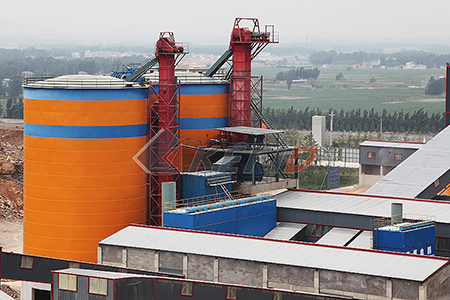
High-temperature ball milling: An efficient method to
2024年3月1日 This study proposed high-temperature ball milling (HTBM) to modify irregular titanium and its alloys powder for AM, such as hydrogenation-dehydrogenated titanium (HDH Ti), and the ball milling mechanism was revealed. The results showed the irregular HDH Ti powder gradually turning into nearly spherical and flake structures.
More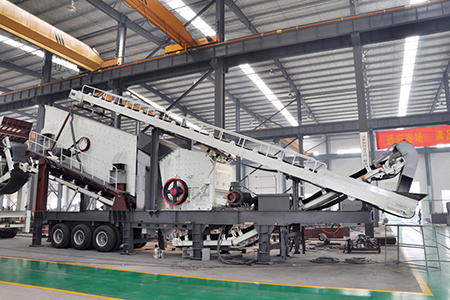
Effects of ball milling on powder particle boundaries and
The Cu-0.25 wt% Al powder was prepared by water atomization, followed by internal oxidation, diffusion, and reduction. Dispersion-strengthened copper powders with internal nano-Al 2 O 3 were obtained as starting materials. The initial powders were ground via a high-energy planetary ball mill with a ball-to-powder weight ratio of 3:1 for 1 h.
More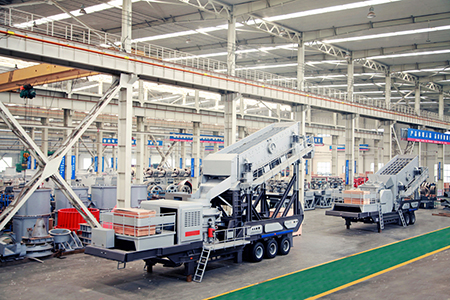
Direct Mechanocatalysis: Using Milling Balls as Catalysts
2020年4月21日 High-speed ball-milling: Direct mechanocatalysis is a new catalysis concept using high speed ball milling conditions. The surface of the milling balls is the catalytic active site, hence the recovery of the catalyst is convenient and efficient. Being a solid state technique, solvent related problems are omitted.
More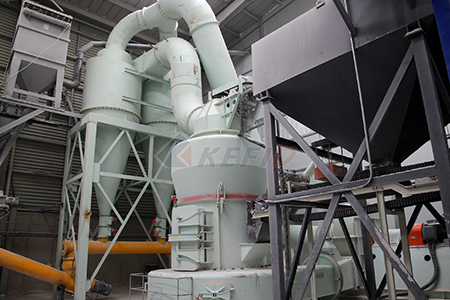
Aromatic substitution in ball mills: formation of aryl chlorides
Aryl chlorides and bromides are formed from arenes in a ball mill using KHSO5 and NaX (X = Cl, Br) as oxidant and halogen source, respectively. Investigation of the reaction parameters identified operating frequency, milling time, and the number of milling balls as the main influencing variables, as these de.
More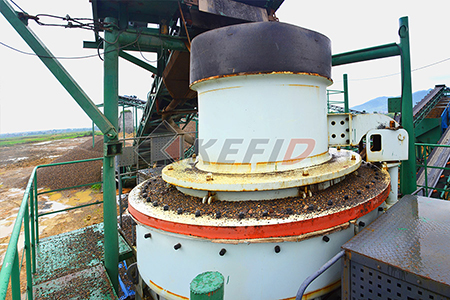
(PDF) Producing Metal Powder from Machining Chips Using Ball
2023年6月27日 Nevertheless, parameter factors, such as the type of ball milling, ball-to-powder ratio (BPR), rotation speed, grinding period, size and shape of the milling media, and process control agent...
More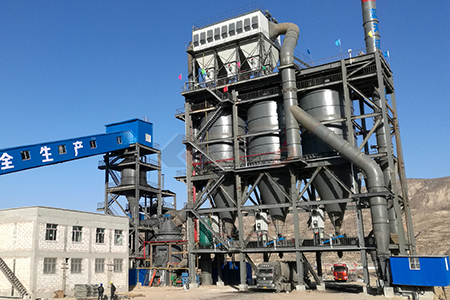
Producing Metal Powder from Machining Chips Using Ball
2023年6月27日 The optimum ball mill parameters to achieve a small particle size of 0.056 µm include a ball mill speed of 500 rpm, a milling time of 10 h, and a ball-to-powder ratio (BPR) of 10:1. These settings are sufficient for obtaining better results.
More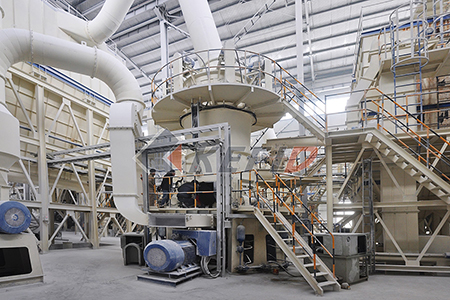
Mechanochemical preparation of single atom catalysts for
2023年3月1日 In this review, we systematically summarized the methodology and principle of ball milling strategy for the preparation of SACs for the first time, which include the solvent-assisted ball-milling strategy, solvent-free ball-milling strategy, and ball-milling abrasion-thermal atomization joint strategy.
More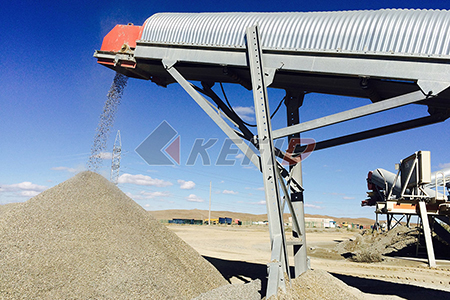
Materials Development Using High-Energy Ball Milling: A
2022年6月17日 High-energy ball milling (HEBM) of powders is a complex process involving mixing, morphology changes, generation and evolution of defects of the crystalline lattice, and formation of new phases.
More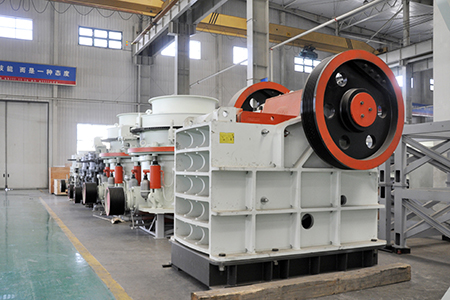
Ball milling process variables optimization for high-entropy
2023年9月1日 In this study, the influence of ball milling variables (PCA type, PCA amount, ball milling time, and ball milling speed) on the onset of solid-solution, grain size, and particle size of a model HEA (AlCoCrFe) is systematically evaluated.
More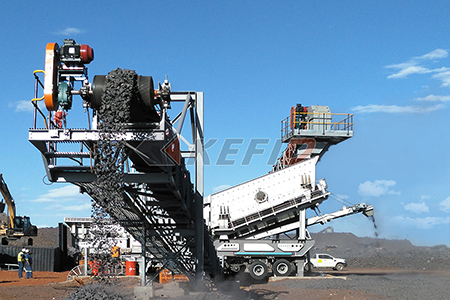
Control the Mechanochemical Energy of Ball Milling To
2023年10月3日 According to collision theory and the strength of materials, it was calculated that the glass would not be broken by ball milling at 146 r/min. Due to mechanochemistry reactions of organic pollutants on the surface, a large number of hydroxyl and ethylenic bond groups were decomposed, producing harmless organic gases, such as propane and ethyl ...
More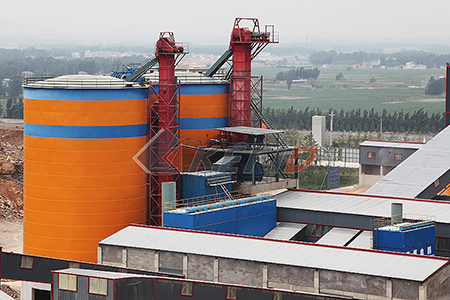
High-temperature ball milling: An efficient method to
2024年3月1日 This study proposed high-temperature ball milling (HTBM) to modify irregular titanium and its alloys powder for AM, such as hydrogenation-dehydrogenated titanium (HDH Ti), and the ball milling mechanism was revealed. The results showed the irregular HDH Ti powder gradually turning into nearly spherical and flake structures.
More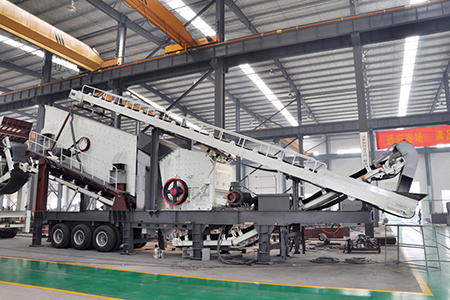
Effects of ball milling on powder particle boundaries and
The Cu-0.25 wt% Al powder was prepared by water atomization, followed by internal oxidation, diffusion, and reduction. Dispersion-strengthened copper powders with internal nano-Al 2 O 3 were obtained as starting materials. The initial powders were ground via a high-energy planetary ball mill with a ball-to-powder weight ratio of 3:1 for 1 h.
More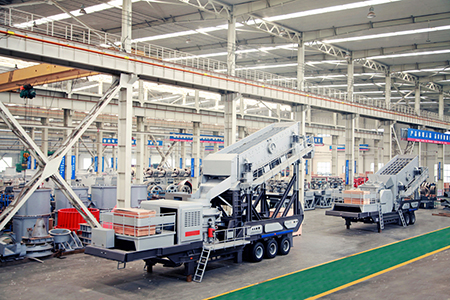
Direct Mechanocatalysis: Using Milling Balls as Catalysts
2020年4月21日 High-speed ball-milling: Direct mechanocatalysis is a new catalysis concept using high speed ball milling conditions. The surface of the milling balls is the catalytic active site, hence the recovery of the catalyst is convenient and efficient. Being a solid state technique, solvent related problems are omitted.
More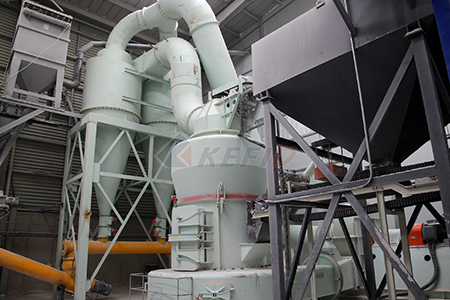
Aromatic substitution in ball mills: formation of aryl chlorides
Aryl chlorides and bromides are formed from arenes in a ball mill using KHSO5 and NaX (X = Cl, Br) as oxidant and halogen source, respectively. Investigation of the reaction parameters identified operating frequency, milling time, and the number of milling balls as the main influencing variables, as these de.
More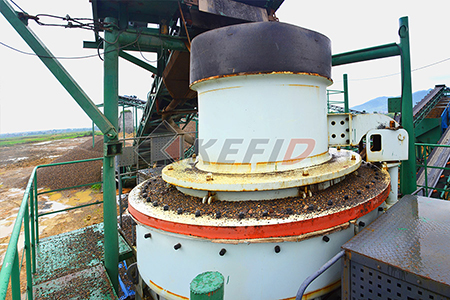
(PDF) Producing Metal Powder from Machining Chips Using Ball
2023年6月27日 Nevertheless, parameter factors, such as the type of ball milling, ball-to-powder ratio (BPR), rotation speed, grinding period, size and shape of the milling media, and process control agent...
MoreParties De La Machine De Concasseur De Pierre
- broyeur à cylindres de sable de silice en Congo
- processo de moagem por difusorprocesso de moagem tintas
- réseau de connaissances sur les broyeurs
- fonds de prevoyance mines de charbon
- concasseur pulvérisateur de pierre indiana
- concasseur de charbon mobile à vendre angola
- de fonctionnement du convoyeur
- concasseur marteaux vendeur medan indon sie
- concasseur et Viper cone
- mobiles pierre utilisee broyeur de pierres pierre
- importateur et exportateur de concasseur à cône
- petite usine de lavage trommel mini
- pour la machine de concassage
- le traitement du minerai par mousse de flottation des minerais de fer
- broyeur de pierres de bagian TON