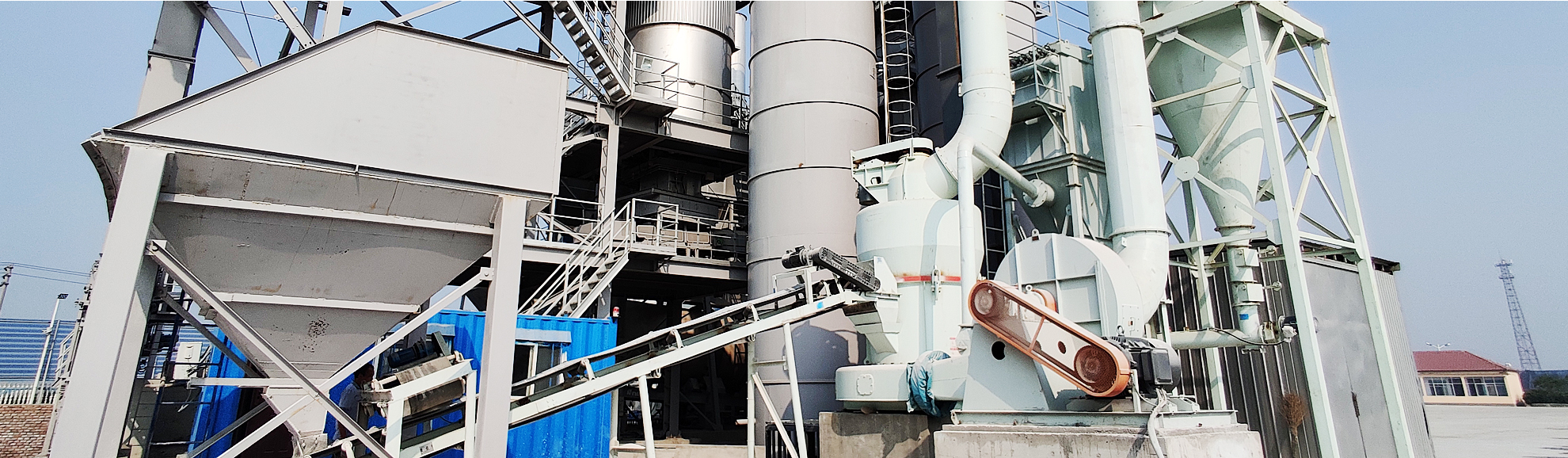
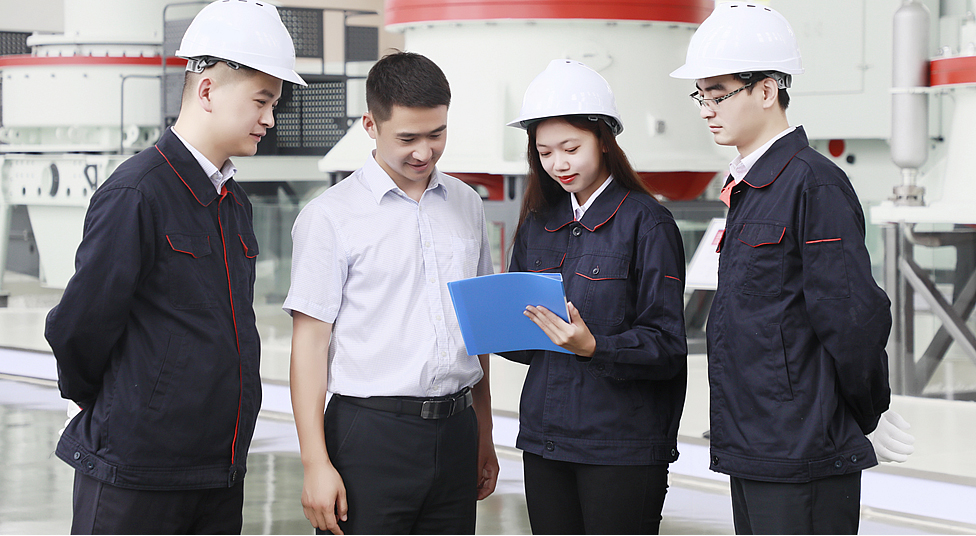
ore filling to power consumption in ball mills Rechercher
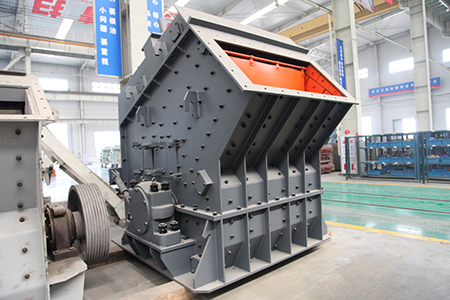
Charge behaviour and power consumption in ball mills: Sensitivity
2001年8月1日 In this paper, combined with shear impact energy model (SIEM) and discrete element method (DEM), the particle collision energy spectrum was applied to analyze the
More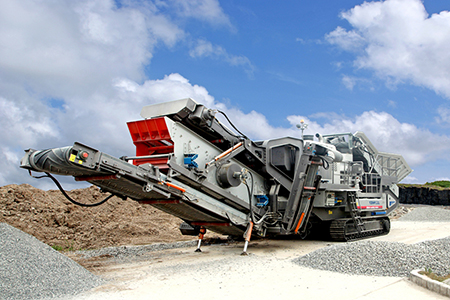
(PDF) Power consumption management and simulation
2022年3月15日 Various operational parameters, such as mill speed, the ball charge composition, charge filling, lifter type, and lifter number, significantly impact ball milling grinding efficiency [3].
More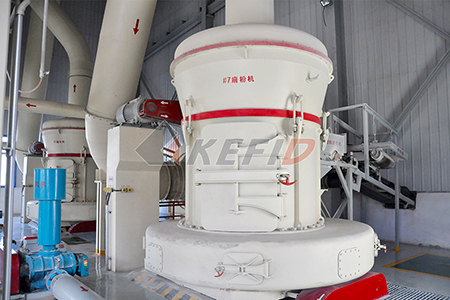
(PDF) Grinding Media in Ball Mills-A Review - ResearchGate
2023年4月23日 Comminution includes the blasting, crushing, and grinding of ore to liberate valuable mineral particles. It consumes most of the energy used in mineral processing plants
More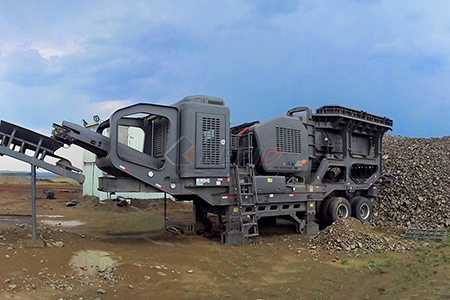
Optimization of Ball Mill Grinding of a Limestone-Type Brecciated ...
2023年4月13日 The effect of ball size and interstitial filling on the performance of dry ball mill grinding was investigated for a limestone-type brecciated uranium ore. The optimum grinding
More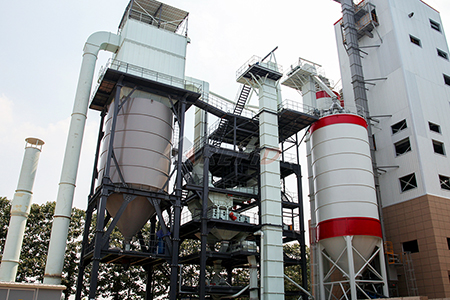
Energy Efficiency Analysis of Copper Ore Ball Mill Drive Systems
Abstract: Milling is among the most energy-consuming technological stages of copper ore processing. It is performed in mills, which are machines of high rotational masses. The start of
More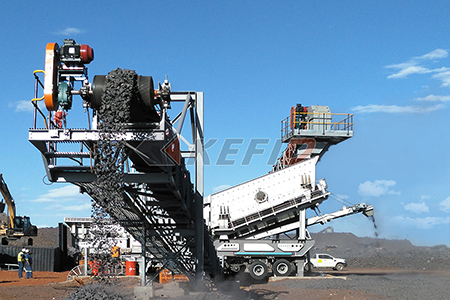
Charge behaviour and power consumption in ball mills: sensitivity
2001年8月1日 In this research, the effect of ball size distribution on the mill power draw, charge motion regime and breakage mechanism in a laboratory ball mill was studied using the
More
Ball charge loading - impact on specific power consumption and
2006年5月30日 The research concludes that lowering the ball mill filling percentage negatively affects mill sizing and increases capital and installation costs of milling equipment.
More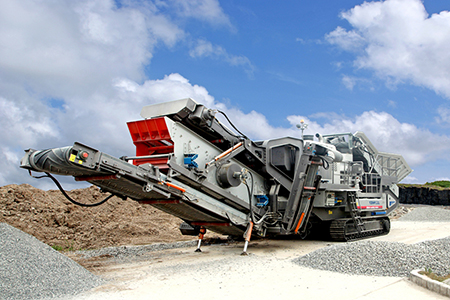
A Review of the Grinding Media in Ball Mills for Mineral Processing
2023年10月27日 Grinding media play a vital role in enhancing the efficiency of a ball mill through their direct effect on the breakage rate, mill load behaviour, power draw, and general
More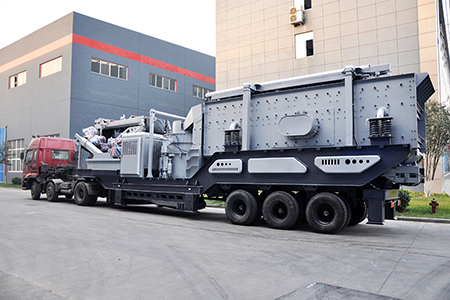
Improvement of methods to ensure energy efficiency of ball mills ...
2023年8月21日 The main way to improve the performance of ball mills is to optimize the operating modes of the electric drive and mill equipment, to ensure stable operation of the
More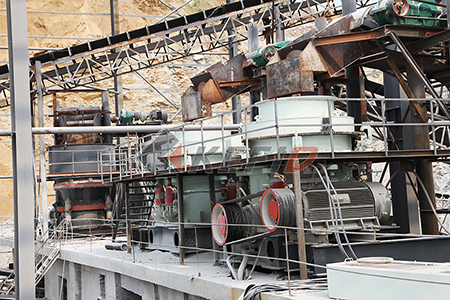
Charge behaviour and power consumption in ball mills:
2001年8月1日 Request PDF Charge behaviour and power consumption in ball mills: Sensitivity to mill operating conditions, liner geometry and charge composition Discrete element method (DEM) modelling has ...
More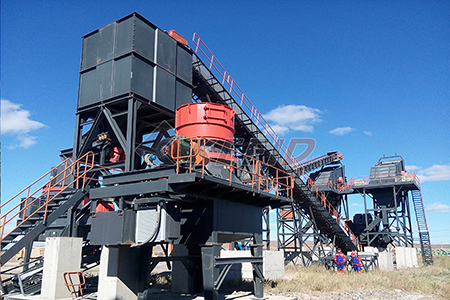
Effect of lifters and mill speed on particle behaviour, torque, and ...
Abstract Crushing and grinding consume most of the energy in mineral processing. Ball mill is an important kind of grinding equipment used to decrease the size of ore particles. The power consumption of a ball mill is one of the most important parameters to consider in the design of a ball mill because it determines its economic efficiency. The power consumption is usually
More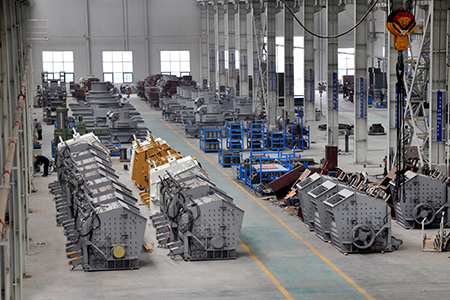
Inventory Of Common Faults And Solutions Of Mining
5 天之前 Reason: This is a common problem mining ball mills face, resulting in low productivity and low ore processing efficiency. One reason may be the improper design of the grinding chamber, which affects the flow of materials
More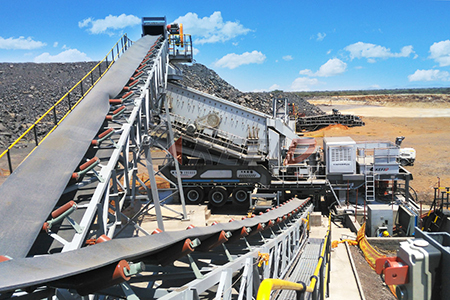
Improvement of methods to ensure energy efficiency of ball mills ...
2023年8月21日 In this study, the Bond (1961 ) approach and the Morrell (1996) approach proposed forthe prediction of the power of wet ball mills, autogenous mills and semi-autogenous mills were tested.
More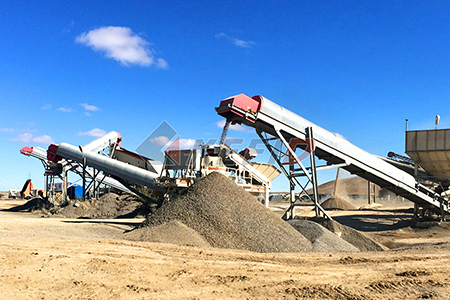
(PDF) Effects of Ball Size Distribution and Mill Speed and Their ...
2020年7月2日 When the mills charge comprising 60% of small balls and 40% of big balls, mill speed has the greatest influence on power consumption. When the mill charge is more homogeneous size, the effect of ...
More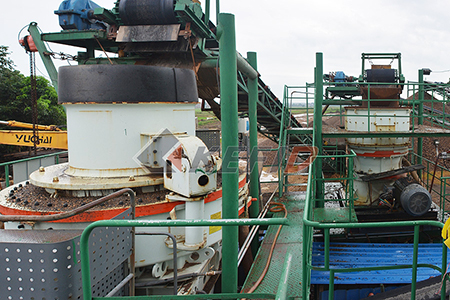
Consumption of steel grinding media in mills – A review
2013年8月1日 Apart from these cost factors, one of the major unsolved problems in the optimal design of ball mills concerns the equilibrium media size distribution in the mill, which is determined by the rate at which make-up media is added to the mill, as well as the rate at which these grinding media are consumed (Austin and Klimpel, 1985).Reliable prediction of grinding
More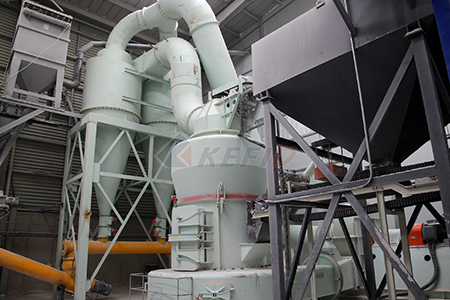
Energy Saving and Consumption Reduction in Ball Mills
2024年10月15日 The use of alumina ceramic grinding balls in ball mills improves ore dissociation, ... and decrease power consumption. (6) ... The second-stage ball mills number 5, with a filling rate of 35%.
More
Charge behaviour and power consumption in ball mills:
2001年8月1日 Discrete element method (DEM) modelling has been used to systematically study the effects of changes in mill operating parameters and particle properties on the charge shape and power draw of a 5-m ball mill. Specifically, changes in charge fill level, lifter shape (either by design or wear) and lifter pattern are analysed. The effects of changes to the properties of the
More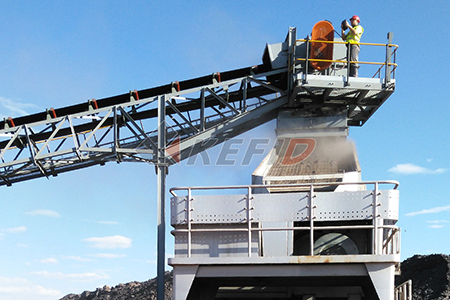
Scale-up of power consumption in agitated ball mills
Mathematical models are presented which describe the power consumption in agitated ball mills in absence of grinding beads. In addition, tests with grinding beads filling were also performed, leading to scale-up guidelines with respect to power consumption. Finally, the influence of size and material of grinding beads was investigated.
More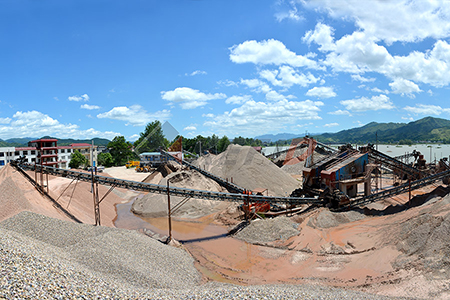
Ball Milling - 911Metallurgist
2017年4月22日 Ball consumption varies with the fineness of the product, hardness of the ore, quality of ball, and whether a mill is run in closed or open circuit. The ball, consumption for mills delivering a coarse product, all passing 8-mesh- and containing 10 to 20 per cent. below 200-mesh, the mill being run in open circuit, is about ½ lb. per ton for steel balls and 1 lb. for
More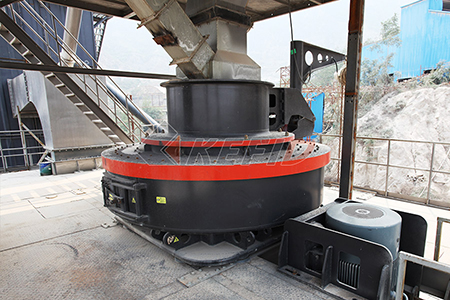
comparison of power consumption in iron ore wet and dry ball mill
Ball Mill Reducing Power Consumption In Ball Mill Wikipedia. Power Saving Measures For Cement Millscement. Jul 08 2019 01 measures to reduce power consumption from a process perspective 1 the design and selection of the mill is a key factor in general replacing a small mill with a large mill can increase production and save electricity and replace the ball mill with low
More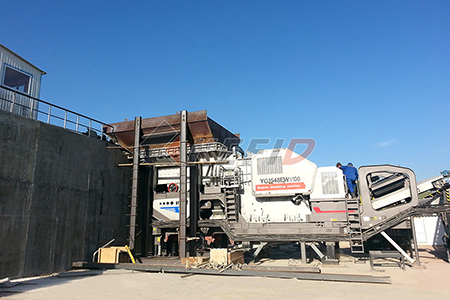
Factors Affecting Ball Mill Grinding Efficiency
2017年10月26日 The following are factors that have been investigated and applied in conventional ball milling in order to maximize grinding efficiency: a) Mill Geometry and Speed – Bond (1954) observed grinding efficiency to be a function of ball mill diameter, and established empirical relationships for recommended media size and mill speed that take this factor into
More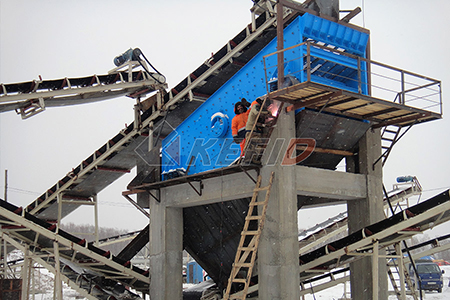
Effect of lifters and mill speed on particle behaviour, torque, and ...
2017年5月1日 Crushing and grinding consume most of the energy in mineral processing. Ball mill is an important kind of grinding equipment used to decrease the size of ore particles. The power consumption of a ball mill is one of the most important parameters to consider in the design of a ball mill because it determines its economic efficiency.
More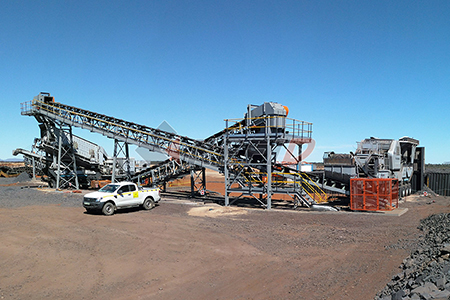
Grinding Media Wear Rate Calculation in Ball Mill
2017年4月29日 In the previous discussion the fact was established that the work done by a ball when it strikes at the end of its parabolic path is proportional to its weight and velocity; then, since the velocity may be considered as constant for all the balls in the mill, the work done by a ball is proportional to its weight. Since the amount of ore crushed varies as the work done upon it, it
More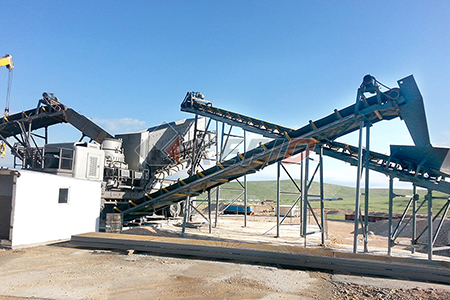
Modelling Power Consumption in Ball-End Milling Operations
2011年5月10日 Power consumption is a factor of increasing interest in manufacturing due to its obvious impact on production costs and the environment. The aim of this work is to analyze the influence of process parameters on power consumption in high-speed ball-end milling operations carried out on AISI H13 steel.
More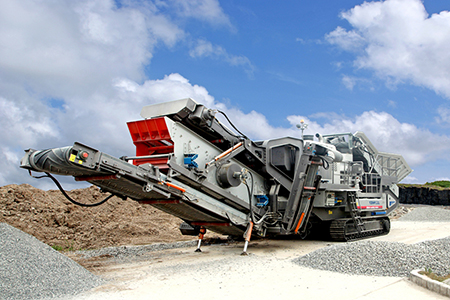
How to effectively reduce the energy consumption of ball mill
2024年4月22日 In order to reduce the power consumption of the ball mill, ... Reasonable steel ball filling rate. When the speed of the ball mill reaches a certain level and the filling rate is large, the steel balls will hit the material more times, ... Application of wet rod mill in 150tpd tungsten ore project.
More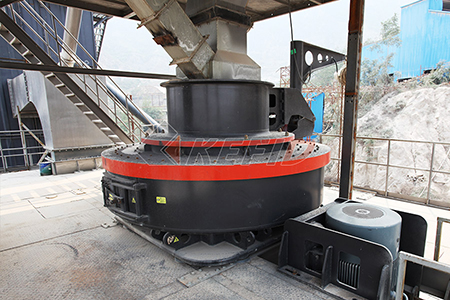
Heat generation model in the ball-milling process of a tantalum ore
2017年2月1日 from the boundary of a ball mill from the load: (i) direct heat transfer from the l oad to wall, (ii) h eat transfer from the air to the wall, and (iii) heat transfer between the load and the gas.
More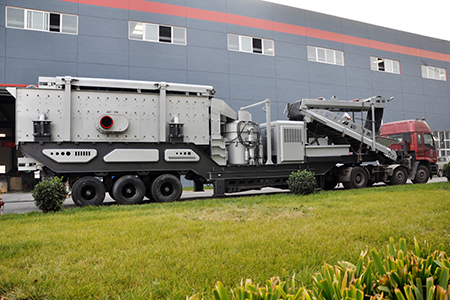
Understanding fine ore breakage in a laboratory scale ball mill using ...
2011年2月1日 The feed (ore) size distribution used was also chosen to match the feed that would typically be used in such a ball mill test. It is relatively fine with a top size of 2.8 mm.This distribution has been truncated at 1.18 mm to keep the simulation size under 1 million particles in order to make the computational duration manageable.The effect of this cut off size will be
More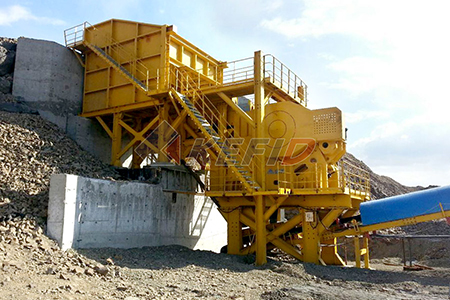
How to reduce the energy consumption of ball mill - LinkedIn
2021年6月2日 1. Change the grindability of ore The grindability of the material fed into ball mill is one of the reasons that affect the energy consumption of ball mill.
More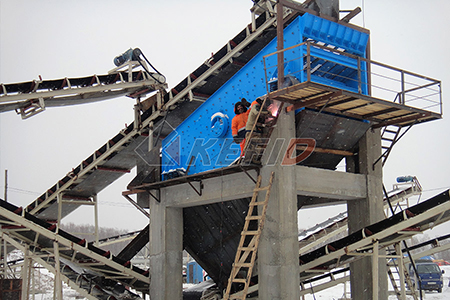
Charge behaviour and power consumption in ball mills:
Discrete element method (DEM) modelling has been used to systematically study the effects of changes in mill operating parameters and particle properties on the charge shape and power draw of a 5-m ball mill. Specifically, changes in charge fill level, lifter shape (either by design or wear) and lifter pattern are analysed. The effects of changes to the properties of the charge
Moretrituradores de pedra de carboneto de tungstenio
- coût de l usine de valorisation du minerai de fer
- ciment concassage machine machine ciment concasseur fabricants
- broyeur à boulets en inde industrie des cimenteries
- tonne par heure concasseur roule afrique du sud
- tout sur les concasseurs à cônes
- Clay broyage primaire
- l usine de concassage mobile de pointe
- système de raffinage pour le tantale
- équipement de concassage mobile d or en indonésie
- concasseur de pierre immediatement
- carriere de pierre ou de l extraction de sable
- desalignement de broyeurs a marteaux
- 4254s modèle wsm marteaux broyeur
- machine de traitement quary
- affaires de concassage de pierre kabrai